Дипломная работа: Технологический процесс изготовления вала насоса
4. В области выбора средств технологического оснащения (СТО):
·
Оборудование –
универсальное, в том числе с ЧПУ, специализированные;
·
Приспособления –
универсальные, стандартные, нормализованные,
специализированные;
·
Режущие
инструменты – стандартные, нормализованные, специальные;
·
Средства контроля
– универсальные, специальные
5. В области проектирования технологических операций:
·
Содержание
операций – одновременная обработка нескольких поверхностей, исходя из
возможностей оборудования;
·
Загрузка
оборудования – периодическая смена детали на станках, коэффициент закрепления
операций от 10 до 20;
·
Расстановка
оборудования – по группам станков, предметно замкнутые участки;
·
Настройка станков
– по измерительным инструментам и приборам или работа без предварительной
настройки по промерам.
6. В области нормирования технологического процесса:
·
Определение
режимов резания – по общемашиностроительным
нормативам и эмпирическим формулам;
·
Нормирование –
детальное пооперационное;
·
Квалификация
рабочих – средняя;
·
Технологическая
документация – маршрутные и операционные карты.
Принятой стратегией будем руководствоваться при разработке технологического
процесса изготовления вала.
2.2
Выбор и проектирование заготовки
Задача данного
подраздела - выбрать методы получения заготовки и обработки поверхностей,
обеспечивающих минимум суммарных затрат на получение заготовки и ее обработку.
2.2.1 Выбор метода
получения заготовки
Учитывая конструкцию
изготавливаемого вала и материал заготовки – сталь 30ХМ, можно предложить два
основных альтернативных метода получения заготовки:
1. Прокат;
2. Штамповка на ГКМ.
1. Прокат
По ГОСТ 2590-71 определим диаметр прутка для данной заготовки:
1)
определим припуск
на механическую обработку шейки вала наибольшего диаметра:
, (2.3.)
где Dдmin – наименьший предельный размер
расчетной ступени по чертежу, мм;
2 Zomin – расчетный минимальный общий
припуск на обработку по диаметру, мм;
Определим значение минимального припуска после
каждой операции по формуле:
, (3.3)
где Rz , h, мм – высота неровностей и дефектный слой, образовавшиеся на
обрабатываемой поверхности при предыдущей обработке;
Di
,мм- суммарное значение пространственных отклонений;
eуi,мм -
погрешность установки.
Суммарное значение пространственных отклонений определим по формуле:
(3.4)
где Dк.о. –общая кривизна заготовки
(учитывается на первой операции механической обработки);
Dсм -
величина смещения заготовки, т.к. обработка ведется в патроне за величину
смещения принимаем отклонение от соосности.
Общая кривизна заготовки:
(3.5)
где Dк – удельная изогнутость и коробление
заготовки, мкм/мм;
l –
длина заготовки, мм. Так
как допустимая кривизна реза прутка не должна превышать 5 мм, длина заготовки составляет 209,5 мм.


Погрешность установки для однопозиционной обработки:
(3.6)
где eб – погрешность базирования;
eз –
погрешность закрепления.
Так как при обработке диаметра измерительные и технологические базы
совпадают, погрешность базирования eб
= 0 при всех установках заготовки.



2)
по рассчитанному
диаметру определяем ближайший диаметр заготовки из сортового проката: Dз = 95 мм.
Для проведения в дальнейшем технико-экономического обоснования выбора
заготовки необходимо определить коэффициент использования материала для данного
метода.
Коэффициент использования материала определим по формуле:
Ки1=q/Q, (2.2.)
где q – масса детали, q = 2,56 кг (см. п. 2.1.1.);
Q-
масса заготовки
Объем заготовки: 
Зная объем детали и плотность материала, определяем массу заготовки:

Подставив полученные значения масс детали и заготовки в формулу 2.2.,
получим коэффициент использования материала для отрезки из проката: Ки1=2,56/11,653=0,22.
2. Штамповка на ГКМ
Ведем расчет поковки по ГОСТ 7505-89.
Исходные данные для расчета.
Ориентировочная величина расчетной массы поковки, кг:
(2.2.)
где МД –масса детали, кг;
Кр – расчетный коэффициент, устанавливаемый в соответствии с
приложением 3 (табл.20).

Класс точности – Т5 ( приложение 1).
Группа стали – М1 (табл.1).
Степень сложности – С3 (приложение 2).
Конфигурация поверхности разъема штампа – П (плоская) (табл.1)
Исходный индекс – 9 (табл.2).
По табл. 3 ГОСТ 7505-89 определяем припуски на механическую обработку,
рассчитываем размеры поковки и их допустимые отклонения, учитывая
дополнительные припуски, по табл. 8 ГОСТ 7505-89 назначаем допуски поковки. Все
значения вносим в таблицу 2.1.
Таблица 2.1 Допуски и припуски на
размеры поковки
Размер
детали, мм
|
Поверхн-ти,
на которые
назначается припуск
|
Допуск
на размер
поковки, мм
|
Припуск,
мм
|
Расчет размера
поковки
|
Окончатль-ный
размер (учитывая округления до 0,5 мм) |
Æ87 |
2 |
1,4 |
1,4 |
Æ87+2×(1,4+0,3+0,4) |
Æ91
|
Æ63 |
4 |
1,4 |
1,4 |
Æ63+2×(1,4+0,3+0,4) |
Æ67
|
Æ45 |
11 |
1,4 |
1,5 |
Æ45+2×(1,5+0,3+0,4) |
Æ50
|
19,5 |
33 |
1,2 |
1,3 |
19,5+(1,3+0,3+0,4) |
21,5
|
21 |
5 |
1,2 |
1,4 |
21+(1,4+0,3+0,4) |
23
|
Остальные
требования по ГОСТ 7505-89 |
Дополнительные припуски, учитывающие:
смещение по поверхности разъема штампа - 0,3 мм (табл.4);
изогнутость и отклонения от плоскости и от прямолинейности – 0,4 мм
(табл.5);
Радиус закругления наружных углов – 4,0 мм (табл.7).
Штамповочный уклон - 7Å (табл.18).
Для проведения в дальнейшем технико-экономического обоснования выбора
заготовки необходимо определить коэффициент использования материала для данного
метода. Коэффициент использования материала определим по формуле 2.2.
Объем заготовки определяем как алгебраическую сумму объемов тел за
вычетом полых цилиндрических составляющих и сегментов, входящих в конфигурацию
заготовки:

Зная объем детали и плотность материала, определяем массу заготовки:

Подставив полученные значения масс детали и заготовки в формулу (2.2.),
получим коэффициент использования материала для ковки на горизонтально-ковочных
машинах: Ки2=2,56/4,86=0,53.
Для окончательного решения по
выбору метода получения заготовки, следует провести сравнительный экономический
анализ по технологической себестоимости.
2.2.2 Экономическое обоснование выбора метода получения заготовки
Оценку эффективности различных вариантов получения заготовок чаще всего
проводят по двум показателям:
а) коэффициенту использования материала заготовки (см. формулу 2.2.)
б) технологической себестоимости изготовления детали. Сюда включаются
только те статьи затрат, величины которых изменяются при переходе одного варианта
к другому.
На стадии проектирования технологических процессов оптимальный вариант
заготовки, если известны массы заготовки и детали, можно определить путем
сравнения технологической себестоимости изготовления детали, рассчитанной по
формуле:
Sтд = Sзаг·Q + Sмех(Q-q) - Sотх(Q-q), (2.3.)
где Sзаг –стоимость одного кг заготовки,
руб/кг;
Sмех – стоимость механической обработки,
отнесенная к одному кг срезаемой стружки, руб/кг;
Sотх – цена 1 кг. отходов, руб/кг, Sотх = 0,0144 руб/кг;
Sмех = Sс + Ен·Sк , (2.4.)
где Sс – текущие затраты на 1 кг стружки, руб/кг;
Sк – капитальные затраты на 1 кг стружки, руб/кг;
По табл. 3.2 [Технология отрасли] для автомобильного и
сельскохозяйственного машиностроения Sс = 0,188
руб/кг, Sк = 0,566 руб/кг.
Ен – нормативный коэффициент эффективности капитальных
вложений, Ен = 0,15.
Смех = 0,188 + 0,15·0,566 = 0,273 руб/кг.
Это значение принимаем для обоих методов получения заготовки.
Стоимость заготовки, полученной методом проката:
, (2.5.)
где М – затраты на материал заготовки, руб
, (2.6.)
где Q –масса заготовки, кг;
S
–цена 1 кг материала заготовки, руб;
q –
масса готовой детали, кг;

где SСо.з.
– технологическая себестоимость операций правки, калибрования прутков, разрезки
их на штучные заготовки:
, (2.6.)
где Сп.з. – приведенные затраты на рабочем месте, руб/ч;
Тшт(ш-к) – штучное или штучно-калькуляционное время выполнения
заготовительной операции (правки, калибрования, резки и др.).
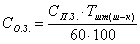
Подставим рассчитанные значения в формулу (2.)
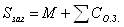
Стоимость заготовки, полученной методом ковки на ГКМ с достаточной для
стадии проектирования точностью можно определить по формуле:
Сзаг = Сi/1000
× kт × kc× kв× kм× kп, (2.5.)
где Сi - базовая
стоимость одного 1 т поковки, полученной на ГКМ, руб.:
Сi = 0,725 руб;
kт – коэффициент, зависящий от класса
точности, для поковок нормального класса точности:
kт = 1;
kc – коэффициент, зависящий от группы
сложности поковки, для третьей группы сложности:
kc =1,0;
kв – коэффициент, зависящий от марки
материала и массы поковки, для стали 40Х при массе поковки менее 10 кг:
kв =0,8;
kм – коэффициент, зависящий от марки
материала поковки, для стали 30ХМ:
kм = 1;
kп – коэффициент, зависящий от объема
производства поковок и группы серийности:
kп = 1;
Подставим определенные значения в формулу (2.5.):
Сзаг = Сi/1000
× kт × kc× kв× kм× kп
Подставим полученные данные в формулу (2.3) и рассчитаем технологическую
себестоимость изготовления детали, для двух методов получения заготовки:
-для проката:
Стд1 = 0,29×3,12+ 0,273 × (3,12-2,2) - 0,0144×(3,12-2,2)= 1,143 руб.;
- для штамповки на ГКМ:
Стд2 = 0,821×2,64+ 0,273 × (2,64-2,2) – 0,0144×(2,64-2,2) = 2,281 руб.
Расчеты проведены в ценах 1985 года. Для учета ценовой инфляции введем
коэффициент К = 10000. Тогда стоимость заготовки:
-для литья в земляные формы Сзаг1=0,298×10000=2980 руб;
-для литья в оболочковые формы Сзаг2=0,821×10000=8210 руб.
Полная себестоимость с учетом коэффициента инфляции составит:
-для литья в земляные формы Стд1=11430 руб;
-для литья в оболочковые формы Стд2=22810 руб.
Вывод: по результатам проведения сравнительного анализа технологической
себестоимости двух методов получения отливки можно заключить, что экономически
целесообразнее использовать при получении заготовки детали метод ковки на
горизонтально-ковочной машине, т.к. полная себестоимость получения заготовки
этим методом существенно ниже чем методом отрезки сортового проката.
Экономический
эффект при изготовлении детали из заготовки полученной ковкой на ГКМ, по
сравнению с изготовлением детали резкой сортового проката для годовой программы
выпуска-15000 шт. составит:
Э=(Стд2
- Стд1)·N=
(22810-11430)·15000=170700000руб.
Страницы: 1, 2, 3, 4, 5, 6, 7, 8, 9, 10, 11, 12, 13, 14, 15, 16
|