Реферат: Смазка оборудования на металлургических предприятиях
Примечание:
d—внутренний диаметр.
Допускаемые
скорости подшипников качения при использовании пластичной смазки определяют из
соотношения внутреннего диаметра d,
мм и частоты вращения ω, мин-1. Практически же окружная
скорость вращения не должна превышать 4—5 м/с. Однако для этой цели существуют
определенные формулы.
Подшипниковые
узлы необходимо тщательно защищать от попадания пыли, грязи и воды. В противном
случае долговечность подшипников резко снижается. Для защиты подшипников
разработаны и успешно эксплуатируются специальные уплотнения. В связи с этим
следует помнить некоторые рекомендации по ходовым зазорам в лабиринтных и
других уплотнениях вала. Они изменяются в зависимости от конструкции и во
многом зависят от механической точности, вибрационного перемещения вала в
подшипнике и они необходимы во избежание фрикционного контакта на высокой
скорости. Для неответственных конструкций подшипниковых опор размер этих
зазоров колеблется в пределах от 0,076 до 0,127 мм на радиус и почти столько же
в осевом направлении.
При
назначении жидкого смазочного материала для узлов трения (подшипников качения)
следует иметь в виду, что они весьма чувствительны к количеству подаваемого в
них масла и периодичности его подачи в подшипники. Так, для очень низких
скоростей при d*ω=
10000 и температуре не выше 50 °С достаточно одной-двух капель масла для
нескольких тысяч часов работы подшипника.
Если
же требуется достичь минимального значения момента трения (при том же
произведении d*ω=
10000), следует использовать масло с меньшей вязкостью, чем это было до этого
Масла
для подшипников качения (и скольжения тоже), заключенных в общий картер с зубчатыми
передачами (редукторы), подбираются в первую очередь исходя из требований по
смазыванию зубчатых передач, однако и с учетом эффективности смазывания
подшипников.
Смазывание
погружением можно успешно применять до значения d*ω
=
100000 (при условии соблюдения необходимого низкого уровня масла в ванне с
жидким смазочным материалом) При применении смазывания погружением важно
поддерживать в процессе эксплуатации правильный уровень масла в ванне
подшипника. Этот уровень должен находиться между 1 /3 и 1/2 высоты нижнего
шарика или ролика подшипника, поскольку даже небольшое повышение уровня масла в
ванне приводит к повышению коэффициента трения и температуры подшипника. Об
этом свидетельствует следующее экспериментальное исследование. Повышение уровня
масла в ванне подшипника от центра нижнего шарика до его верхней точки вызывает
сильный нагрев подшипника (эквивалентный повышению частоты вращения подшипника
в 2—2,5 раза или увеличению радиальной нагрузки от 2 до 6 раз, а иногда и
более. При d*ω
≤
200000 рекомендуется капельное смазывание, при котором к поверхностям трения
жидкий смазочный материал подводится в виде капель.
При
d*ω
≈
600000 и когда температура может достигать 150 ˚С многие пластичные смазки
оказываются недостаточно работоспособными, а иные могут оставаться годными к
работе не более нескольких сотен часов. В связи с этим при высоких скоростях
необходимо в зону трения подавать только чистое смазочное масло, питая
подшипники методом капельного смазывания или смазывания под давлением, при
котором смазочный материал подводится к поверхностям трения под давлением. При
необходимости может быть использовано смазывание масляным туманом, при котором
смазочный материал подводится к поверхностям трения в виде легкого или густого
тумана, обычно образуемого путем введения смазочного материала в струю воздуха
или газа. Кроме того, следует предупреждать возникновения разности воздушного
давления (в корпусе подшипника и за его пределами), для чего могут
потребоваться специальные уплотнения. Следует применять только определенные
уплотнения, которые обеспечивают надежную работу подшипников, в частности
лабиринтные уплотнения. Необходимо также использовать корпуса подшипников с
минимальным воздушным пространством.
Капельное
смазывание является наилучшим методом смазывания для подшипниковых опор
металлургического оборудования. Оно обеспечивает довольно устойчивое охлаждение
и исключает турбулентное сопротивление подшипника, как весьма ответственного
узла оборудования отрасли. Однако если по каким-либо причинам (например, по
условиям конструкции) нельзя применить капельное смазывание или смазывание под
давлением или смазывание масляным туманом, используют фитильное смазывание, при
котором жидкий смазочный материал подводится к поверхности прения с помощью
фитиля. При этом масло всасывается через подшипник при помощи маслоотражателей
и насосных устройств с целью преодоления сопротивления вращению подшипника.
Часто
используют метод фитильного смазывания. При этом фитили должны иметь
определенные размеры, особенно в поперечном сечении. Они всегда должны быть
погруженными в масло. Их следует использовать парами и располагать как можно
ближе к подшипнику. Если большая площадь фитилей хорошо окружает вал, то они
способны вновь поглощать масло, которое при работе отбрасывается от вала.
Вязкость смазочного масла должна быть такой, чтобы его можно было подавать к
фитилям при низких температурах при давлении ниже атмосферного и пониженных
скоростях. При этом маслоотражатели должны пропускать через подшипник масляный
туман, а маслосборники должны тщательно охлаждаться.
При
больших нагрузках и высоких скоростях (d*ω
>
600000) рекомендуют осуществлять капельное смазывание подшипников. Если же
имеется источник сухого и чистого воздуха, а некоторая потеря смазочного масла
не имеет существенного значения, тогда нужно использовать смазывание
подшипников масляным туманом. При этом в линии подачи воздуха в таких системах
устанавливают воздухоотделитель и фильтр, для чего необходимо тщательно
охлаждать маслосборник, чтобы маслоотражатели легко.
Смазка
плоских направляющих скольжении и качения.
Направляющие
прямолинейного движения являются разновидностью опор скольжения или качения.
Они обеспечивают прямолинейность возвратно-поступательного движения деталей
(типа столов, суппортов и ползунов) и их применяют главным образом в станках, а
также поршневых и кузнечнопрессовых машинах. Основным критерием
работоспособности направляющих скольжения (рис. 3) является износ и заедание. Для
уменьшения износа применяют ёсмазочный материал, защиту от загрязнения,
износостойкие материалы (сталь,чугун, антифрикционные материалы и пр.), а также
используют малые давления на поверхностях трения. В качестве антифрикционных
материалов используют бронзы и баббиты.
На
рис. 3 показаны две плоские пластины А и Б, залитые маслом и нагруженные силой
Р. Под действием силы О пластина А движется относительно пластины Б со скоростью
υ. Если последняя мала (рис. 3, а), то пластина А соскабливает масло с
пластины Б, в результате чего поверхности трения (А и Б) непосредственно
соприкасаются друг с другом. При этом образуется полусухое (граничное) или полужидкостное
трение При достаточно большой скорости v
(рис. 3, б) пластина А поднимается в масляном слое и принимает наклонное
положение, подобно тому как поднимается глиссер, скользящий по поверхности
воды. В результате между пластинами образуется сужающийся зазор, в который
непрерывно затягивается вязкое и липкое масло. Протекание масла через
сужающийся зазор сопровождается образованием давления р (см. рис. 3, б),
которое уравновешивает внешнюю нагрузку. В этом случае движение продолжается в
условиях жидкостного трения. Переход к режиму гидродинамического трения
происходит при некоторой скорости, называемой критической υкр.
Смазка
канатов и цепей.
Кашпы
смазываются на месте их производства для предохранения от коррозии (этот процесс
называется пропиткой) и уменьшении трения между стренгами канатов в процессе их
эксплуатации (этот процесс называется смазыванием). Смазываются канаты жидкими
ипластичными смачочными материалами. Это практически понужидкие смачочные
материалы CТП-JI
(летом) и СТП-З (зимой) и высоковязкое смачочное масло, которым в данном случае
является трансмиссионное масло для промышленного оборудования-нигрол (ТУ 38
101529—75). Кроме того, можно использовать полугудрон, осевые масла Л и 3.
В
качестве канатных смазок применяют смазку БОЗ (ТУ 399-157—75), торсиол-38 (ТУ
38 УССР 201214—80), торсиол-55 (ГОСТ 20458—75). В качестве заменителей
используют высоковязкое масло, солидол С.
В
процессе работы цепной передачи шарнирные соединения цепи находятся в условиях
большого истирания и сильного износа. Плохо смазываемая цепь быстро выходит из
строя в виду разработки отверстий в пластинках, что приводит к увеличению шага
цепи и общей ее длины и к нарушению зацепления цепи со звездочками. В то же
время из большого опыта эксплуатации цепных передач известно, что цепные
передачи или собственно цепи, находясь в масляных ваннах, безотказно служат в
течение восьми и даже более лет. Особенно опасен износ в условиях абразивной
среды. Так, смазка
деталей втулочно-роликовых цепей маслом в условиях абразивного материала
(запыления) ведет к интенсивному износу вследствие непрерывного поступления
вместе со смазочным материалом частиц абразивного материала в зазор между
трущимися поверхностями звеньев. При работе в запыленной среде наименьшему
абразивному изнашиванию подвергаются цепи, работающие без смазочного материала.
При работе же цепей в смазочном материале частицы абразивной пыли непрерывно
поступают в зазоры, попадают в смазочный материал во взвешенном состоянии и
циркулируют между валиком и роликом цепи, интенсивно их изнашивая.
|
|
|
|
|
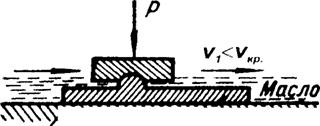 |
|
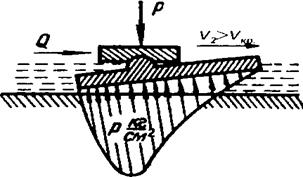 |
|
Цепи
смазывают жидкими и пластичными смазочными материалами. Масла следует подбирать
в зависимости от температуры среды, скорости и метода смазывания.
Пластичные
смазочные материалы для цепных передач подбирают в зависимости от температуры
среды, а также влажности окружающего воздуха. Так, в частности, при температуре
до 60 С и большой влажности применяют солидол С или УС-2 или графитный
смазочный материал УСсА. При температуре выше 60 °С и отсутствии влажности
используют консталин жировой или синтетический. Цепи смазывают погружением их в
пластичную смазку, предварительно разогретую до температуры не более 55 ˚С.
Особенности
смазки узлов трения оборудования для металлургических предприятий, работающих в
условиях низких и высоких температур
Вопрос
подбора смазочного материала для узлов трения, работающих в условиях низких (-15)-(-20
°С) и высоких (70— 100 °С) температур, не простой. Естественно, что здесь
необходимы специальные смазочные материалы. В частности, удовлетворительная
работа узлов трения при высоких температурах в основном достигается двумя
способами: применением специальных смазочных материалов и нанесением
специальных смазочных покрытий на трущиеся поверхности. Покрытия в данном
случае играют роль сухого смазочного материала. В качестве смазочного покрытия
могут служить покрытия галоидные, керамические, из нитрида бора и сернистые. К
ним относятся следующие химические соединения: дисульфиды молибдена, титана,
урана, циркония, оксид свинца, диселенид вольфрама (WSe2).
Кроме того, смазочную роль выполняют различные пластмассы и графит. Этой же
цели можно достичь, если использовать никелирование и хромирование. Как пример
галоидного покрытия можно привести воздействие паров йода на поверхность
детали, выполненной из титана. При этом образуется пленка диоксид йодистого
титана, которая сохраняет свою работоспособность при температуре до 400 °С.
Простейшим
керамическим покрытием является оксидная пленка, которая образуется на
поверхности металла при нагреве ее на воздухе или в кислороде. Следует
отметить, что детали с таким покрытием могут работать до температуры порядка
800 С, а покрытия нитридом бора выдерживают температуры свыше 1000 °С. По своим
антифрикционным свойствам нитрид бора напоминает графит.
Минимальный
коэффициент трения обеспечивают сернистые покрытия из дисульфида молибдена (MоS2),
сернистый титан (TiS), дисульфиды
урана (US2)
и циркония (ZrS2).
Детали, покрытые этими соединениями, могут работать при температуре порядка
600—900 °С. При температурах порядка 530—540 ˚С весьма эффективным
смазочным материалом является окись свинца (РьО). Однако следует помнить, что
при более низкой температуре применение РьО затруднено, поскольку окись свинца
переходит в Рь3О4, коэффициент трения у которого
значительно выше. Хорошими смазочными свойствами обладает дисетенил вольфрама (WSe2).
При работе в узле трения пленка постоянно переходит с одной поверхности трения
на другую. Кроме того смазочная пленка постоянно затягивает разрывы.
Для
специфичных условий работы можно рекомендовать следующие смазки: твердую
антифрикционную смазку ВНИИ НП-203 (ТУ 38 10186—75), пасты ВНИИ НП-225 (ГОСТ
19782—74), ВНИИ НП-232 (ГОСТ 14068—79), свинцоль-02 (ТУ 38 — 101578—76), ВНИИ
НП-242 (ГОСТ 20421—75), ВНИИ НП-254 (ТУ 38—40146—83). В этих смазках содержится
дисульфид молибдена, что придает им высокие смазочные способности.
Соответственно дисульфид молибдена и технический графит содержат
антифрикционные пластичные смазки ВНИИ НП-220 (ТУ 38 — 101475—74) и ВНИИ НП-231
(ТУ 38—01113—76), что отличает их высокие смазочные свойства.
В
частности, для горячих резьбовых соединений, работающих до температур порядка
400 С, рекомендуются ВНИИ НП-225 и ВНИИ НП-232. Для матриц и штампов
рекомендуется порошок MoS2.
Накатка пленки из пасты ВНИИ НП-232 или масло с добавлением порошка Мо52 — для
шестерен, зубчатых реек. Для греющихся подшипников качения используют смазки
ВНИИ НП-232 и ВНИИ НП-242. Паста ВНИИ НП-232 используется также для смазывания
роликов, шестерен, трансмиссий, подшипников скольжения. Смазки и пасты
наносятся на очищенные и обезжиренные поверхности.
Для
смазки шестерен, подшипников, цепных передач, резьбовых соединений при
температуре от -20 до +120 С можно использовать минеральное масло с добавкой от
1 до 5% MoS2.
Дело в том, что дисульфид молибдена выдерживает большие давления в зоне трения.
В отсутствие воздуха MoS2
не окисляется при температурах до 1000—1100 °С. По данным информации США.
известно применение пластичной смазки на основе дисульфида молибдена и
модифицированной формы бентонитовой глины. Такая смазка работоспособна при
рабочем давлении до 700 МПа, ее можно применять для непрерывно работающих машин
при температурах 230—232 °С. Она пригодна для смазывания деталей, работающих во
влажных условиях и даже условиях водяного пара высокого давления. Изменяя
состав смазки, можно добиться такой ее рецептуры, когда она будет пригодна для работы
в условиях, в которых невозможно применение масел и смазок на обычной нефтяной
основе. Эти смазочные материалы можно применять и для смазки узлов трения
агломерационных машин.
Резюмируя
сказанное, отметим лишь, что смазка ВНИИ НП-225 работает в условиях от —30 до
+350 °С, используется для смазывания бронзовых вкладышей, резьбовых соединений,
прокладок из естественной и искусственной резины. В интервале температур от -20
до +120 °С работает смазка ВНИИ НП-232. Она используется для смазывания
зубчатых передач, резьбовых соединений, пальцев и винтов. В интервале
температур от —35 до 120 °С работоспособна смазка ВНИИ НП-242. Ее применяют для
смазывания шариковых и роликовых подшипников при высоких нагрузках. Для
смазывания шариковых и роликовых подшипников тяжелонагруженных электрических
машин при температурах от -60 до +150 °С применяют смазку ВНИИ НП-220.
Следует
отметить, что твердые смазочные материалы не могут вытеснить обычные смазочные
материалы и нужны только в тех случаях, когда использование обычных смазочных
материалов не дает удовлетворительных результатов. Применять их лучше в виде
паст, суспензий и присадок к пластичным смазочным материалам.
В
качестве антифрикционного материала для узлов трения широкое распространение
приобретают фторопласты и особенно фторопласт-4 (политетрафторэтилен или ПТФЭ).
Эффективно применение этого материала в среде химически активных веществ как
самосмазывающегося антифрикционного материала для подшипников скольжения,
элементов уплотнительных устройств и т. п. Дело в том, что чистый фторопласт-4
обладает низкой теплопроводностью, высокой хладотекучестью и высоким
коэффициентом линейного расширения. Все это ограничивает область его
применения. Однако стоит в него ввести наполнитель и сразу же картина меняется.
Наполнители в составе фторопласта резко изменяют все его свойства и приводят к
существенному уменьшению износа самого материала. В качестве наполнителей
обычно используют дисульфид молибдена, нитрид бора (BN),
сернокислый барий (BaSO4),
тальк, газовую сажу и коллоидный графит (от 10 до 45%).
При
высоких нагрузках и температурах хорошо показали себя в работе металлические
подшипники, поверхности трения которых покрыты слоем полнтетрафторэтиленовой
смолы. В отсутствии смазочного материала они могут выдерживать большие нагрузки
при малых скоростях. Прибавление подкладки из волокнистой ткани делает их
работоспособными без смазывания при температуре до 290 ˚С. Причем они в
пять раз работают дольше, чем аналогичные металлические подшипники со
смазыванием. Они способны нести нагрузку до 170—225 МПа. Упомянутые покрьтия
состят из двух слоев, соединенных вместе. Внутренний слой состоит из волокна
политетрафторэтиленовой смолы, тканного вместе со стеклянным волокном, а
наружный слой состоит из стеклянного волокна, пропитанного смолой. Толщина слоев
около 0,33 мм. Подшипники обеспечиваются уплотнением. Посадка подшипника на вал
осуществляется с первоначальным нагягом (около 0,05 мм). Все эти мероприятия
существенно увеличивают долговечность подшипника.
БИБЛИОГРАФИЯ
Евдокимов
А. Ю. Смазочные материалы и проблемы экологии. Москва «Высшая школа», 1999.
Школьникова
В. М. Топливо, смазочные материалы и технологические жидкости. Москва «Высшая
школа», 1998.
Фукс
И. Г. Пластические смазки. Москва «Высшая школа», 2002.
Гаевик
Д. Т. Смазка оборудования на металлургических предпреятиях. Москва, 2000.
|