Курсовая работа: Проектирование индивидуального привода
Условие
прочности втулки на смятие:

допускаемое напряжение на смятие для твердых сортов
резины.
8.
СОСТАВЛЕНИЕ ВЕДОМОСТИ ПОСАДОК СОПРЯЖЕНННЫХ РАЗМЕРОВ
Выбор
посадок посадочных мест подшипников.
В
редукторе применяю подшипники 0 класса точности. Посадки колец
шарикоподшипников выбираю от вида нагружения – циркуляционного:
-
внутреннего кольца на вал – L0/k6;
-
наружного кольца в корпус – N7/L0.
Выбор
посадок зубчатых колес
Зубчатые
колеса насаживаю на вал по посадке r6 по системе отверстия 7-го квалитета точности – Н7/r6.
Выбор
посадок шкивов ременной передачи
Шкивы
ременной передачи на вал насаживаю по посадке jS6 по системе отверстия 7-го квалитета
точности – Н7/jS6.
Выбор
посадок крышек торцовых узлов на подшипниках качения
Крышки
торцовые устанавливаю в корпусе и крышке редуктора по посадке Н7/Н8.
Ведомость
посадок сопряженных размеров
№ |
Сопрягаемые детали |
Диаметр и посадка сопряжения |
Количество сопряжений |
Примечания |
1.
|
Вал-подшипник |
35 L0/k6 |
2 |
|
2.
|
Корпус-подшипник |
72 N7/L0 |
2 |
|
3.
|
Вал-подшипник |
50 L0/k6 |
2 |
|
4.
|
Корпус-подшипник |
90 N7/L0 |
2 |
|
5.
|
Вал-подшипник |
60 L0/k6 |
2 |
|
6.
|
Корпус-подшипник |
110 N7/L0 |
2 |
|
7.
|
Вал-шкив |
32 H7/jS6
|
1 |
|
8.
|
Вал-муфта |
55 H7/n6 |
1 |
|
9.
|
Крышка-корпус |
72 H7/h8 |
2 |
|
10.
|
Крышка-корпус |
90 H7/h8 |
2 |
|
11.
|
Крышка-корпус |
110 H7/h8 |
2 |
|
12.
|
Вал-зубчатое колесо |
45 H7/r6 |
1 |
|
13.
|
Вал-зубчатое колесо |
55 H7/r6 |
1 |
|
14.
|
Вал-зубчатое колесо |
65 H7/r6 |
1 |
|
9.
СИСТЕМА СМАЗКИ РЕДУКТОРА
Поскольку
окружная скорость зубчатых колес до 12…14 м/с, то смазку осуществляю путем
погружения зубчатых колес в масло, заливаемое внутрь корпуса. Глубину
погружения колес в масло принимаю равной 0,12 радиуса окружности выступов
большего колеса: 70 мм.
Поскольку
редуктор двухступенчатый выбираю сорт масла по вязкости, равной среднему
арифметическому из рекомендуемых значений кинематической вязкости масел.
Выбираю
масло с вязкостью v= 81.5 cCт – масло индустриальное И20 по ГОСТ
20799-75.
Для контроля уровня
масла в корпусе редуктора применяю жезловый маслоуказатель. Объем масленой
ванны составляет приблизительно 3,5 дц3.
Смазка
подшипников валов осуществляется тем же маслом, что и зубчатые колеса. Смазка
осуществляется разбрызгиванием.
10.
РАСЧЕТ КЛИНОРЕМЕННОЙ ПЕРЕДАЧИ.
Исходные
данные:
P1= 4.56 кВт; n1= 1450 мин-1;
Р2=Р1/η1=4,56/0,96=4,75
кВт; n2=496,5мин-1; u=2.92; T1=30.25 H∙м;
T2=87,72 H∙м.
Сечение
ремня и размеры сечения.
Выбираю
сечение А ремня с площадью поперечного сечения F=81 мм2; табл. 2.2.1 [4].
Минимальный
расчетный диаметр ведущего шкива d1min=90 мм. Однако для обеспечения
большей долговечности ремня выбираю шкив большего диаметра, а именно d1=160 мм.
Диаметр
ведущего шкива:

Ближайшее
стандартное значение 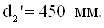
Действительное
передаточное число проектируемой передачи:

Пересчитываю
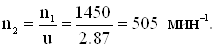
Расхождение
с заданным:
(при
допускаемом до 3%). Принимаю диаметры шкивов .
Минимальное
межосевое расстояние (2.2.5 [4])
;
Hp=8 (табл. 2.2.5 [4]):

Принимаю
близкое к среднему а’= 500 мм.
Расчетная
длина ремня (2.2.6 [4])

Действительная
длина ремня, мм;

Lp=2000 мм.
Межцентровое
расстояние:
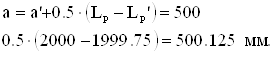
Принимаю
а= 500 мм.
Коэффициент,
учитывающий длину ремня:
СL=1,1 (табл. 2.2.6).
Угол
обхвата ремнем меньшего шкива:

сα=0,95.
Скорость
ремня:

Число
ремней передачи:

ср=0,87.
Р0=2,67
кВт (табл. 2.2.7 [4]).
ck = 0.8…0.85 (т. 2.2.5) при предварительно принятом z=2.
Сила,
нагружающая валы передачи:
принимаю
напряжение от предварительного натяжения:
;
предварительное
напряжение:
;
Рабочее
натяжение ведущей ветви:

Ведомой:

Окружное
усилие:
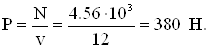
Усилие
на валы:

Конструирование
шкивов.
Исходные
данные.
Диаметры
шкивов:
; .
Число
ремней: .
Сечение
ремня: А; F= 81 мм2.
Выбираю
материал шкивов и размеры ступиц.
Ведущий
шкив – назначаю СЧ15 ГОСТ 1412-85.
Ведомый
– СЧ15 ГОСТ1412-85, так как v= 12 м/с до 30 м/с.
Согласно
принятому электродвигателю и расчетов, произведенных ранее, диаметры валов под
шкивом:
; диаметр
ступицы:
.
Принимаю
.

Принимаю
.
Длина
ступицы:

Принимаю
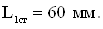
Наружный
диаметр шкивов:


Ширина
венца:

Другие
размеры шкивов.
Шкив
ведущий:
.
Принимаю
.
.
Принимаю
,
где
;

Принимаю
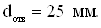
Шкив
ведомый.
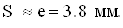
Принимаю

Число
спиц:

Принимаю
n= 4шт.
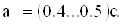
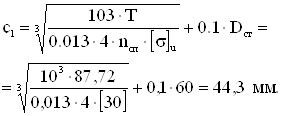
Принимаю




Шероховатость
поверхности:
-
отверстие ступицы Ra= 1,6 мкм;
-
боковые поверхности ступиц Ra=
3,2 мкм.
Допуски
формы и расположения.
Радиальное
и осевое биение:
ведущего
– 0,12; 0,1
ведомого
– 0,16; 0,25.
Допустимый
дисбаланс шкивов 4 г∙м.
11
ЗАКЛЮЧЕНИЕ
При
выполнении курсового проекта по “Деталям машин” было выявлено, что:
1.
Материалы зубчатых колес для тихоходной передачи выбраны верно, поскольку при
проверочном расчете по контактным напряжениям выполняется условие:

А
по напряжениям изгиба:

Имеется
незначительный запас прочности. Материалы для зубчатых колес быстроходной
передачи согласно проверочному расчету можно было выбрать с меньшими
прочностными характеристиками, поскольку
и
для
быстроходных передач такая ситуация является характерной, поэтому материалы для
зубчатых колес быстроходной передачи оставлю прежними.
2.
При расчете тихоходного вала выявилось, что общий коэффициент запаса прочности
незначительно превышает допускаемый запас прочности:
,
что
свидетельствует о том, что материал вала можно было выбрать с более низкими
прочностными характеристиками.
3.
При выборе подшипников №212 для тихоходного вала необходимая динамическая
грузоподъемность
Стр=
30 кН < С= 40,3 кН.
Это
говорит о том, что можно было выбрать подшипник более легкой серии, но таких
подшипников нет в ГОСТе 8338.
12.
СПИСОК ИСПОЛЬЗОВАННЫХ ИСТОЧНИКОВ
1.
Чернавский С.А.,
Ицкович Г.М., Боков К.Н., Чернин И.М. и др. «Курсовое проектирование деталей
машин» – М., «Машиностроение», 1979 г.
2.
Иванов М.Н.,
Иванов В.Н. «Детали машин. Курсовое проектирование. Учебное пособие для
машиностроит. вузов» – М., «Высш. школа», 1975 г.
3.
Чернин И.М.,
Кузьмин А.В., Ицкович Г.М. «Расчет деталей машин. Справочник» – Мн., «Вышэйшая
школа», 1974 г.
4.
Курмаз Л.В.,
Скойбеда А.Т. «Детали машин. Проектирование. Учебное пособие» - 2-е издание
исправленное и дополненное, - Мн., УП «Технопринт», 2002 г.
5.
Методические
указания «Детали машин» (Расчетно-графическая работа №3) – Могилев, 2002 г.
|