Курсовая работа: Технологический процесс изготовления детали
[2,
с.66, табл. 4.7.],
где - погрешность коробления.
- величина смещения отверстия равна
допуску на диаметр заготовки.
мкм;
мкм на 1 мм диаметра [2,
с. 71, табл. 4.8.]
мкм.
мкм.
Пространственные
отклонения на размеры отверстия после механической обработки определяем по
формуле:
[2,
с. 73],
где - коэффициент уточнения.
После чернового
растачивания:
мкм;
после чистового
растачивания:
мкм;
после тонкого
растачивания:
мкм.
Погрешность закрепления в
4-хкулачковом патроне при черновом растачивании мкм
[2, с. 75, табл. 4.10].
Погрешность установки
[2, с.74], но у нас = 0. Тогда:
мкм.
Погрешность установки при
чистовом растачивании (базирование по ранее расточенному отверстию):
мкм [2,
с. 79, табл. 4.12.].
Для тонкого точения:
мкм [2,
с. 79, табл. 4.12.].
Величина минимального
припуска:
для чернового
растачивания:
мкм;
для чистового
растачивания
мкм;
для тонкого растачивания
мкм.
Определяем расчётные
размеры:
для тонкого растачивания
равен минимальному размеру диаметра на детали [9, с. 14] мм.
для чистового
растачивания определяется по формуле:
[9, с.14],
по этой же формуле
определяются размеры после чернового растачивания и для литого отверстия.
После чистового
растачивания:
мм;
после чернового
растачивания
мм
для литья
мм.
Далее производим
округление расчётных размеров до того знака десятичной дроби, с каким дан
допуск на размер данной операции – это будут минимальные значения размеров.
Максимальные операционные
размеры определяем по формуле:
; [9,
с. 15],
то есть за счёт
прибавления допусков к минимальным размерам.




Вычерчиваем схему
расположения припусков и допусков при обработке отверстия (см. рисунок 6.1.).
Остальные припуски на
обрабатываемые поверхности заготовки выбираем по ГОСТ 26545 – 85 [10] и
подсчитываем размеры заготовки. Допуски размеров определяем по таблице 1 [10].
Таблица 6.2
Размер, мм |
Допуск, мкм |
Размер, мм |
Допуск, мкм |
1 |
2 |
3 |
4 |
300 |
10 |
140 |
8 |
340 |
10 |
295 |
10 |
R35 |
5,6 |
205 |
9 |
170 |
9 |
185 |
9 |
160 |
9 |
195 |
9 |
165 |
9 |
310 |
10 |
210 |
9 |
254 |
10 |
Припуски на обработку
определяем по таблице 6 [10]. Для этого нужно предварительно знать ряд
припусков на обработку отливок, что находим в табл. 14. Для степени точности
13Т подходит ряд 6.
Таблица 6.3
Размер детали,
мм |
Припуск, мм |
Размер
заготовки, мм |
1 |
2 |
3 |
170 |
7,5 |
177,5 4,5
|
160 Н7 |
9,3 |
141,4 4,5
|
160 |
9,3 |
150,7 4,5
|
210 |
7,5+5,6 |
223,1 4,5
|
295 |
9,8 |
275,4 5
|
Рассчитанные вручную
припуски совпадают с припусками рассчитанными на ПЭВМ (таблица 6.4). Приступаем
к вычерчиванию заготовки.
6.2 Анализ
и обоснование схем базирования и закрепления
Выбор технологических баз
в значительной степени определяет точность линейных размеров относительно
положения поверхностей, получаемых в процессе обработки, выбор режущих и
измерительных инструментов, станочных приспособлений, производительность
обработки [3, с.109].
Проанализируем варианты
базирования для вертикально-фрезерной операции (020) и горизонтально-расточной
операции (030).
Выполним схему базирования
для операции вертикально-фрезерной, на которой будет производится фрезерование
предварительное плоскости на фланце корпуса. Плоскость будет служить чистовой
базой для выполнения последующих операций. На операцию заготовка корпуса
поступает предварительно обработанная на токарном станке, поэтому в качестве
установленной базы будем использовать торец корпуса. Будучи установленная на
этот торец заготовка лишается трёх степеней свободы (перемещение вдоль оси и
вращения вокруг двух других осей) – установочная база.
Затем в качестве базовой
поверхности будем использовать предварительно обработанное отверстие (размер ). Будучи установленная на
валец этим отверстием заготовка лишается ещё двух степеней свободы (перемещение
вдоль двух осей) – двойная опорная база.
И в качестве черновой
базы будем использовать поверхность двух бобышек. Будучи установленная на
подводимую опору этими бобышками, заготовка лишается последней 6-й степени
свободы (вращение вокруг оси) – опорная база.
Так как, размер
выдерживаемый на операции – расстояние от оси отверстия до обрабатываемой
поверхности на чертеже это размер (170) идёт от одной базы, мы соблюдаем при
базировании принцип совмещения баз, т.е. измерительная и установочная базы
совпадают.
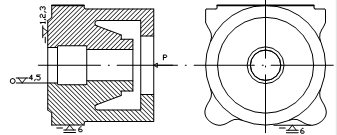
Рисунок 6.2 Схема
базирования и закрепления заготовки на вертикально-фрезерной операции.
Значит, погрешность
базирования на операции будет равна нулю. Зажимную силу нужно направить так,
чтобы она прижимала заготовку к наиболее развитой установочной базе. Схема
базирования и закрепления представлена на рисунке 6.2.
Выполним схему
базирования для операции горизонтально-расточной, на которой будет
производиться сверление и растачивание отверстия Æ85 и Æ90Н12. На операцию заготовка корпуса
поступает предварительно обработанная на фрезерном станке. В качестве
установочной базы будем использовать торец корпуса. Будучи установленная на
этот торец заготовка лишается трёх степеней свободы (перемещение вдоль оси и
вращения вокруг двух других осей) – установочная база.
Затем в качестве базовой
поверхности будем использовать предварительно обработанное отверстие (размер ). Будучи установленная на
валец этим отверстием заготовка лишается ещё двух степеней свободы (перемещение
вдоль двух осей) – двойная опорная база.
Как видно, установочная и
двойная опорная база те же, что и на предыдущей операции. Таким образом,
соблюдается принцип постоянства баз.
И в качестве опорной базы
будем использовать плоскость на фланце корпуса. Будучи установленная на
подвижную опору этой плоскостью, заготовка лишается последней 6-й степени
свободы (вращение вокруг оси) – опорная база.
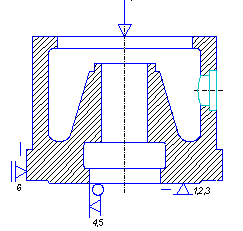
Рисунок 6.3 Схема
базирования и закрепления заготовки на горизонтально-расточной операции.
Так как размер, выдерживаемый
на операции – расстояние от оси отверстия Æ90Н12 до обрабатываемой поверхности (на чертеже это размер
(110)) идёт от торца противоположного установочной базе, принцип совмещения баз
не соблюдается, т.е. измерительная и установочная базы не совпадают. Зажимную
силу нужно направить так, чтобы она прижимала заготовку к наиболее развитой
установочной базе. Схема базирования и закрепления представлена на рисунке 6.3.
Погрешность базирования на размер 110 (расстояние от оси отверстия Æ85 до необрабатываемого торца
заготовки) равна допуску на размер 210 (соединяющий измерительную и
технологическую базы). Размер 210 выполнен по 14 квалитету точности. Значит,
допуск на этот размер равен 1150 мкм [11, табл.2, с.441]. Погрешность
базирования равна 1150 мкм.
6.3
Обоснование выбора металлорежущего оборудования
Выбор типа станка
определяется, прежде всего, его возможностью обеспечить выполнение технических
требований, предъявляемых к обработанной детали в отношении точности ее
размеров, формы и класса шероховатости поверхностей.
В экономике
технологического процесса, весьма большое значение имеет производительность
станка, так как станок должен полностью использоваться по времени. Однако
иногда представляется невыгодным применить станок более высокой
производительности и в том случае, когда загрузка его по времени неполная, если
при этом себестоимость обработки получается ниже, чем на другом станке, хотя бы
и полностью загруженном. В связи с этим следует помнить, что применение специальных,
агрегатных и других высокопроизводительных станков должно быть экономически
обосновано.
На фрезерной операции
используется вертикально-фрезерный станок модели 6Р13.
Технические
характеристики станка модели 6Р13:
Размеры рабочей
поверхности стола (ширина х длина) 400х1600
Наибольшее перемещение
стола:
продольное 1000
Страницы: 1, 2, 3, 4, 5, 6
|