Курсовая работа: Разработка АСР температуры обжига цементного клинкера с циклонным теплообменником
Курсовая работа: Разработка АСР температуры обжига цементного клинкера с циклонным теплообменником
Содержание расчетно-пояснительной записки
Введение
1 Анализ современного состояния автоматизации
технологического процесса обжига цементного клинкера
1.1 Анализ литературных источников
1.2 Автоматизация процесса обжига
цементного клинкера с циклонным теплообменником
1.3 Требования к автоматизированным системам контроля и
управления
2.
Определение параметров объекта регулирования
3. Выбор
типового регулятора АСР и определение параметров его настройки для заданного
технологического параметра
3.1 Определение параметров настройки ПИ - регулятора
4. Анализ
динамических характеристик АСР при выбранном типе
регулятора и найденных параметрах его настройки
5. Расчет
одноконтурной цифровой АСР
6. Выбор технических средств автоматизации
6.1 Датчик температуры
6.2 Регулятор
температуры
6.3 Исполнительный механизм
Заключение
Список используемой литературы
Список аппаратных и программных средств
Приложение 1
Эффективность работы вращающихся печей цементной
промышленности в немалой степени зависит от наладки технологического оборудования,
процесса обжига клинкера и режима эксплуатации печей при выпуске клинкера
высокой активности, минимальном расходе топлива и высоких технико-экономических
показателях.
Комплекс процессов, происходящих во вращающихся печах под
воздействием тепловой энергии, весьма обширен и сложен. Процессы горения
топлива, движения газов и материала, теплообмена и физико-химических
превращений сырьевой смеси тесно связаны между собой и каждый из них имеет
решающее значение. Они и определяют основные мероприятия при проведении наладки:
подбор оптимального химического и минералогического состава клинкера в сырьевой
смеси, обеспечивающего необходимые условия для высокоэффективной работы печи и
стабильности процесса; выбор рациональной конструкции теплообменных устройств для
интенсивного теплообмена и снижения потерь теплоты; отработка рационального
режима сжигания топлива, обеспечивающего экономное его расходование и
интенсивность высокотемпературных процессов; выбор оптимальных режимных
параметров и отработка методов управления процессами.
Производительность печей, удельный расход топлива зависят не
только от конструктивных и технологических исходных характеристик, но и от
режима работы. Форсирование режима до известного предела повышает
производительность, но увеличивает унос материала, температуру отходящих газов,
удельный расход теплоты. Дальнейшее форсирование может привести к сокращению
производительности из-за большого уноса при одновременном резком увеличении
удельного расхода теплоты. Уменьшение нагрузок печей против оптимальных также
расстраивает их работу: происходит смещение зон, пересушка материала и т.д.
Выбор и поддержание оптимальных нормативов, показателей и
параметров технологического процесса оказывает решающее влияние на получение
продукции заданного качества, а также на экономику предприятия.
Обжиг клинкера - самый сложный, важный и энергоемкий передел.
Общие энергозатраты на производство цемента распределяются примерно следующим
образом: подготовка сырья - 10%, обжиг клинкера - 79%, помол цемента - 10%, прочие
- 1%. Поэтому наладка процесса обжига, снижение энергозатрат, прежде всего
затрат топлива приобретают исключительное значение.
В основе наладочных работ лежит анализ процессов,
происходящих в печи при многочисленных изменяющихся факторах. Не следует
полагать, что проведение обычных наладочных работ обеспечит полную оптимизацию
процесса обжига клинкера. Каждый оптимальный режим может быть рассчитан только
с применением средств вычислительной техники на основании достаточно обширной и
точной технической и химико-технологической информации, что требует специальных
исследований.
Совершенствование организаций и методов наладки, испытаний
технологического оборудования, безусловно, способствует повышению технической
культуры его эксплуатации, повышению эффективности цементного производства и
ускорению освоения проектных мощностей предприятий.
Интенсивное развитие цементной промышленности в последние
годы, внедрение печных установок большой единичной мощности, вовлечение в
производственный процесс сырьевых материалов более низкого качества ставят
перед цементным производством новые проблемы.
При обжиге сухих сырьевых смесей используют печи с циклонным
теплообменниками. Размеры таких печей намного меньше размеров печей, работающих
по мокрому способу, так как процессы подготовки сырья вынесены здесь в запечные
агрегаты с интенсивным конвективным теплообменом, обеспечивающим эффективное
использование теплоты отходящих газов. Высокая экономичность, малые размеры и
низкие капитальные затраты при сооружении таких печей обеспечили им широкое
распространение. Благодаря высокой степени декарбонизации сырьевой муки,
поступающей в печь, улучшается ее текучесть и снижается тепловая нагрузка на
печь. Эти особенности в сочетании с простотой регулирования позволяют легко
управлять режимом обжига и обеспечивать надежную работу печного агрегата. На
цементных заводах сухого способа производства успешно эксплуатируются печи с
размерами 4х60, 5х75, 7/6,4х95 м.
Печи для обжига сухих сырьевых смесей при равной
производительности примерно вдвое короче печей для обжига шлама. Это
достигается тем, что часть процессов выносится из печи в запечные теплообменные
устройства. В России для обжига сухих смесей в основном используют печи с
циклонными теплообменниками и с конвейерными кальцинаторами (печи "Леполь").
В основу конструкции печей с циклонными теплообменниками
положен принцип теплообмена между отходящими газами и сырьевой мукой во
взвешенном состоянии. Уменьшение размера частиц обжигаемого материала,
значительное увеличение его поверхности и максимальное использование этой
поверхности для контакта с теплоносителем интенсифицируют процесс теплообмена. Сырьевая
мука в системе циклонных теплообменников движется навстречу потоку отходящих из
вращающейся печи газов с температурой 900...1100°С. Средняя скорость движения
газов в газоходах составляет 15...20 м/с, что значительно выше скорости витания
частиц сырьевой муки. Поэтому поступающая в газоход между верхними I и II ступенями циклонов сырьевая
мука увлекается потоком газов в циклонный теплообменник I
ступени. Поскольку диаметр циклона намного больше диаметра газохода, скорость
газового потока резко снижается и частицы выпадают из него. Осевший в циклоне
материал через затвор-мигалку поступает в газоход, соединяющий II и III ступени, а из него выносится
газами в циклон II ступени. В дальнейшем материал движется
в газоходах и циклонах III и IV
ступеней. Таким образом, сырьевая мука опускается вниз, проходя последовательно
циклоны и газоходы всех ступеней, начиная от относительно холодной (I) и кончая горячей (IV). При этом
процесс теплообмена на 80% осуществляется в газоходах и только 20% приходится
на долю циклонов. Время пребывания сырьевой муки в циклонных теплообменниках не
превышает 25...30 с. Несмотря на это, сырьевая мука не только успевает
нагреваться до температуры 700...800°С, но полностью дегидратируется и на 25...35%
декарбонизируется.
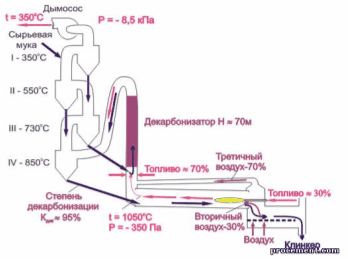
Рис. 1. Схема теплового агрегата для обжига клинкера по
сухому способу.
Перспективность применения сухих печей обусловлена тепловой
экономичностью, высокой удельной производительностью, простотой конструкции,
малыми размерами и низкими капитальными затратами. Недостатки печей этого типа
высокий расход электроэнергии и относительно низкая стойкость футеровки. Кроме
того, они чувствительны к изменению режима работы печи и колебаниям состава
сырья. Поскольку степень декарбонизации цементной сырьевой муки, поступающей из
циклонного теплообменника в печь, не превышает 35%, материал должен оставаться
в печи продолжительное время для завершения процесса обжига. Для интенсификации
процесса разработаны системы трехступенчатого обжига, принцип которого
заключается в том, что между циклонным теплообменником и вращающейся печью
встраивается специальный реактор - декарбонизатор. Сжигание топлива и
декарбонизация материала в таком реакторе происходят в вихревом потоке газов.
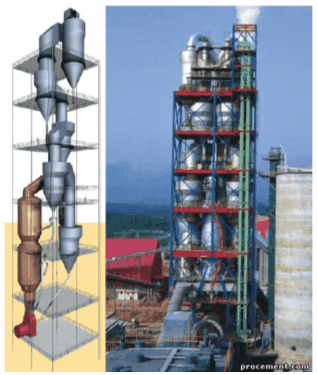
Рис. 2. Модель и реальный вид циклонного теплообменника с
декарбонизатором.
После прохождения циклонных теплообменников сырьевая мука с
температурой 720...750 °С поступает в декарбонизатор. Частицы сырьевой муки и
распыленное топливо диспергируются и перемешиваются. Теплота, выделяющаяся в
результате сгорания топлива, немедленно передается частицам сырьевой муки,
которые нагреваются до температуры 920...970°С. Материал в системе "циклонный
теплообменник - декарбонизатор" находится лишь 70...75 с и за это время
декарбонизируется на 85...95%. Установка декарбонизатора позволяет повысить
съем клинкера с 1 м3 внутреннего объема печи в 2,5...3 раза. Удельный расход
теплоты снижается до 3,0...3,1 МДж/кг клинкера. Кроме того, в декарбонизаторе
можно сжигать низкокачественное топливо, а также бытовые отходы. Стоимость
сооружения установки с декарбонизатором на 10% ниже стоимости установки с
циклонным теплообменником той же производительности. Размеры установки
невелики, и она может использоваться не только при строительстве новых
заводов, но и при модернизации действующих печей.
Вращающиеся печи с циклонными теплообменниками характеризуются
простотой конструкции и соответственно эксплуатации, а также высокой
теплотехнической эффективностью.
Эффективность сухого способа производства, в частности с
использованием вращающихся печей с циклонными теплообменниками, подтверждается
многолетней практикой.
В таблице 1 приведены показатели работы вращающихся печей
цементной промышленности Японии.
Таблица 1
Тип печи |
Средний расход
теплоты на 1 кг
клинкера, кДж
|
Удельная
производительность,
кг/ (м3·ч)
|
Печи с циклонными теплообменниками |
3400 |
64,5 |
Печи с циклонными теплообменниками и декарбонизаторами |
3400 |
97,9 (до 137,5) |
Печи с кальцинаторами типа "Леполь" |
3880 |
58,5 |
Печи мокрого способа |
5520 |
21,9 |
Эти данные показывают, что удельная производительность печей
с циклонными теплообменниками в 3 раза выше, чем печей мокрого способа. Удельная
производительность печей с циклонными теплообменниками на практике в отдельных
случаях более высока ≈73 кг/ (м3·ч), а при осуществлении мер
по повышению частоты вращения может быть доведена до 95,8 кг/ (м3·ч).
Система циклонных теплообменников работает по принципу
противотока горячих газов и материала в системе в целом и прямотока в каждом
цикле. Высокая эффективность теплообмена в циклонных теплообменниках
обеспечивается вследствие непосредственного контакта частиц материала и горячих
газов.
Исследования процесса теплопередачи в системе циклонных
теплообменников позволяют предположить, что основной теплообмен между газами и
материалом протекает в газоходах (≈80%) и только на 20% в циклонах. Основные
параметры газа в системе циклонных теплообменников: скорость в газоходах -
20-22 м/с; расход газа за циклонными 1,4-1,5 м3/кг клинкера; пылеунос
из циклонов 6-9% расхода сырьевой муки. Удельный расход теплоты определяется
многими факторами и уменьшается с увеличением размеров и мощностей печей. Так,
печь с циклонным теплообменниками фирмы "Гумбольдт" при
производительности 350 т/сут. Имеет удельный расход теплоты 920×4,1868, а
при производительности 3500 т/сут. - 740×4,1868 кДж/кг.
Время пребывания сырьевой муки в системе циклонных
теплообменников очень непродолжительно - 25-30 c. За этот короткий промежуток
времени газовый поток отдает теплоту и охлаждается примерно с 1050 до
300-350ºC, а сырьевая мука успевает получить теплоту и нагреться примерно
от 50 до 780-800ºC.
При температуре материала 780-800ºC, степень
декарбонизации составляет 20-25%, при более высокой температуре -
800-810ºC может быть 30-35% и Толька в весьма благоприятных условиях
теплообмена достигает 35-40%.
Однако следует иметь ввиду, что на практике степень декарбонизации
материала, поступающего из циклонных теплообменников в печь, обычно доходит до
40-45%. Это обусловливается выносом из печи прокаленного материала в систему
теплообменников и должно учитываться при наладке процесса и определении
фактической подготовки сырья в запечных теплообменниках.
Циклонными теплообменниками оборудуются короткие вращающиеся
печи (50-70 м). Теплообменники, установленные над загрузочными концами печей,
располагаются один над другим и предназначены подобно конвейерным кальцинаторам
для подогрева и частичной декарбонизации сырьевой смеси. Но в отличие от
конвейерных кальцинаторов материал, подлежащий обжигу в теплообменники,
поступает не в виде гранул, а в виде порошкообразной смеси.
Вращающиеся печи с циклонными теплообменниками из
прямоточных элементов, предложенные Ф. Мюллером, в начале пятидесятых годов
стала выпускать фирма "Гумбольдт" (ФРГ). Вращающиеся печи с
циклонными теплообменниками оказались настолько эффективными, что вслед за
фирмой "Гумбольдт" их стали конструировать и выпускать почти все
зарубежные фирмы, производящие оборудование для цементной промышленности. Наилучших
результатов в отношении экономичности и мощности печей достигли фирмы "Полизиус",
"Ведаг" и "Крупп" (ФРГ). Печи относительно небольшой
производительности выпустили американский филиал датской фирмы "Смидт"
и Пржеровский машиностроительный завод (Чехия).
В настоящее время основное наиболее эффективное и
перспективное направление развития техники производства цементного клинкера
сухим способом состоит в применении и усовершенствовании вращающихся печей с
циклонными теплообменниками.
Цементный клинкер обжигают во вращающихся печах. Вращающаяся
печь представляет собой теплообменный технологический аппарат в виде
вращающегося со скоростью 0,5 - 1 об/мин цилиндра, расположенного на опорах. Благодаря
наклону (3 - 5% к горизонту) и вращению цилиндра на опорах сырьевой материал
непрерывно перемещается в печи. Цилиндр вращается при помощи привода,
устанавливаемого примерно посередине цилиндра.
Современные вращающиеся печи для обжига клинкера, как
правило, оборудованы запечными теплообменниками, в которых осуществляется
подогрев и частичная декарбонизация сырьевой смеси. Расход тепла на обжиг
клинкера составляет 750-850 ккал/кг клинкера. При мокром способе размол
сырьевых компонентов осуществляется в мельницах в присутствии воды, которая
играет роль понизителя твёрдости, интенсифицирует процесс помола и снижает
удельный расход энергии на помол. Полученная сметанообразная масса (шлам) корректируется
до заданного состава и направляется на обжиг. За счёт испарения воды шлама в
печи расход тепла на обжиг увеличивается в зависимости от размера и конструкции
печи составляет 5,45 - 6,7 Мдж/кг (1300-1600 ккал/кг) клинкера. При
комбинированном способе сырьевая смесь готовится по схеме мокрого способа,
затем обезвоживается на вакуум-фильтрах или вакуум-прессах, формуется (обычно в
виде гранул) и поступает на обжиг. Расход тепла при этом составляет около 4,19 Мдж/кг
(1000 ккал/кг) клинкера.
На процесс, происходящий в печи, влияет множество факторов -
количество, влажность, химический состав и тонкость помола шлама (или состав и
количество муки), количество и калорийность топлива, температура и количество
вторичного воздуха, волнообразность движения материала внутри печи и т.п.
Правильному выбору и поддержанию заданного режима работы
печи в значительной мере способствует автоматический контроль и автоматическое
регулирование параметров процесса обжига. В настоящее время печи оснащают
большим количеством приборов контроля и регулирования.
Полная схема системы автоматического контроля и
регулирования печи сложна и громоздка. Ниже рассмотрена упрощенная схема
автоматического регулирования основных параметров печи.
Вращающаяся печь в зависимости от характера процессов,
протекающих в обжигаемом материале на различных ее участках, условно может быть
разделены на зоны сушки, подогрева, кальцинирования, экзотермических реакций,
спекания и охлаждения. Сырьевая смесь, поступающая в печь, в зоне сушки
нагревается до температуры мокрого термометра. Этот участок характеризуется
конвективным теплообменом между дымовыми газами и шламом. Большая часть тепла
расходуется на испарение физически связанной влаги. Материал переходит в
пластичное состояние, а в конце зоны гранулируется. Зона подогрева
характеризуется быстрым ростом температуры до 700º C и дегидратацией
минералов сырьевой смеси. В этой зоне происходит лучистый теплообмен между
футеровкой и материалом, газом и материалом и регенеративный теплообмен через
футеровку.
Страницы: 1, 2, 3
|