Курсовая работа: Процес ручного дугового зварювання
-
внаслідок
малої теплопровідності можливий перегрів зварюваного металу.
Ці сталі
відрізняє підвищена схильність до утворення гартівних структур, а більший, ніж
у низьковуглецевих сталей, коефіцієнт лінійного розширення може викликати
значні деформації і напругу, пов'язані з тепловим впливом дуги. Причому, чим
більше в сталі вуглецю і легуючих домішок, тим сильніше виявляються ці
властивості. Для усунення впливу перерахованих причин на якість зварного
з'єднання рекомендується: ретельно готувати виріб під зварювання; зварювання
вести при великих швидкостях з малою погонною енергією, щоб не допускати
перегріву металу; застосовувати термічну обробку для запобігання утворення
гартівних структур і зниження внутрішньої напруги; застосовувати легування
металу шва через електродний дріт і покриття з метою відновлення домішок, що
вигоряють в процесі зварювання.
Електроди для зварювання
високолегованих сталей виготовляють з
високолегованого зварювального дроту. Застосовують покриття типу Б. Позначення
типів електродів складаються з індексу Э і наступних за ним цифр і букв. Дві
або три цифри, наступні за індексом, указують на кількість вуглецю в металі шва в сотих долях відсотка.
Наступні потім букви і цифри указують приблизний хімічний склад металу. Зварювання проводять постійним струмом
зворотної полярності. При цьому зварювальний струм вибирають з розрахунку 25-40
А на 1 мм діаметру електроду. Довжина дуги повинна бути як можна коротшою.
Рекомендується багатошарове зварювання малого перетину при малій погонній
енергії. Середньолеговані хромовані сталі, такі, що містять до 2% вуглецю,
відносяться до мартенситного класу. Вони зварюються задовільно, але вимагають
підігріву до 200-300 °С і подальшої термічної обробки. Для зварювання
високолегованих сталей і сталей з особливими властивостями
застосовують електроди, стрижні яких виконані із спеціального дроту, по
хімічному складу близькою до зварюваної сталі.
Для
запобігання виникненню міжкристалічної корозії при зварюванні високолегованих
сталей в металі шва створюють двофазну структуру (аустеніт і ферит) для
зменшення зерен, обмежують вміст шкідливих домішок (сірки, фосфору, свинцю,
олова, бісмута), легують титаном, ніобієм, танталом, ванадієм, цирконієм (вони
активно взаємодіють із вуглецем і перешкоджають утворенню карбідів хрому). Крім
того використовують електродні покриття основного та змішаного типу. Для
попередження виникнення тріщин створюють меншу жорсткість виробу, виконують
попередній і супровідний підігрів до 250-300°С, обмежують вміст шкідливих
домішок, уводять легуючі елементи (молібден, марганець, вольфрам), складають
деталі із зазором (1,5-2 мм), зменшують розбризкування металу та об'єм зварної
ванни.
Корозієстійкі
сталі, які не містять титану, ніобію або леговані ванадієм, при нагріванні вище
500°С втрачають антикорозійні властивості. Одержання антикорозійних властивостей, а також підвищеної
пластичності та в'язкості досягають нагріванням металу до 1000-1150°С і швидким
охолодженням у воді (гартуванням). Вміст вуглецю в основному металі до
0,02-0,03% повністю виключає міжкристалітну корозію.
Підігрів
до 100-300°С обов'язковий для мартенситних сталей, а для аустенітних - використовується рідко.
Високолеговані сталі з вмістом вуглецю понад 0,12% зварюються з попереднім
підігрівом до 300°С і вище з наступною термічною обробкою. Шви краще виконувати
тонкими електродами .діаметром 1,6-2,0 мм або електродним дротом діаметром 1,2-2
мм при мінімально можливому зварювальному струмі.
При
зварюванні корозієстійких сталей не допускається збудження дуги на основному
металі і попадання бризок на основний метал. Складки, заглиблення, щілини,
непровари можуть бути джерелом корозії. Кращу корозієстійкість мають гладкі шви
з плавним переходом до основного металу. Не рекомендується зачищати шов
пневматичним зубилом або іншим способом, при яких утворюються вм'ятини, задирки
тощо. Для зменшення вигоряння легуючих елементів зварювання необхідно
виконувати короткою дугою без коливальних рухів кінцем електрода.
Для
зварювання високолегованих сталей і сплавів використовують зварювання
плавленням усіх видів.
Ручне
дугове зварювання покритими електродами виконують при знижених струмах [Ізв
= (15+35)<4], на постійному струмі зворотної полярності, нитковими валиками
без коливальних рухів, короткою дугою. Використовують електроди із стрижнем
такого ж хімічного складу, як і основний метал, з урахуванням показників
зварюваності та експлуатаційних вимог. Наприклад, при зварюванні кислотостійкої
хромонікелевої сталі 12Х18Н10Т для запобігання утворенню гарячих тріщин і
міжкристалічної корозії використовують електроди типу Э-04Х20Н9 (марка ЦЛ-11)
та Э-02Х19Н9Б (марка ОЗЛ-7).
Більшість
високолегованих сталей добре зварюються контактним зварюванням.
2.2 Матеріали, що
використовуються при зварювальних роботах
Поступово ручне
дугове зварювання замінюють напівавтоматичним в атмосфері захисних газів.
Ручне дугове
зварювання плавким електродом виконують за допомогою електродів, які
підрозділяють на типи і марки (ГОСТ 9467-75*).
Електроди для
ручного дугового зварювання є металевий стрижень, на поверхню якого методом
занурення або опресовуванням під тиском наноситься покриття (обмазку) певного складу і товщини. Покриття
повинне забезпечити стійке горіння дуги, отримання металу шва необхідного
хімічного складу і властивостей і ін. Ці вимоги забезпечується матеріалами
електродного стрижня і покриття, до складу яких входять стабілізуючі,
шлакоутворювальні, розкислювальні, легуючі і інші речовини.
Речовини для
покриттів які використовуються для приготування
захисних електродних покриттів можуть бути класифіковані на наступні групи:
Шлакоутворювальні
- мінеральні речовини, що містять оксиди металів (руди): титанову руду (ільменіт),
збагачену титанову руду (титановий концентрат), природний двоокис титану
(рутил), марганцеву руду (піролюзит), польовий шпат, плавиковий шпат, крейду,
фарфорову глину (каолін), кварц, мармур.
Титанова і
марганцева руди збільшують швидкість твердіння шлаку, що особливо важливе при
зварюванні вертикальних і стельових швів. Титанова руда також збільшує
швидкість плавлення електроду, що підвищує продуктивність зварювання. Польовий
шпат збільшує стійкість горіння дуги, але при цьому підвищує рідкотекучість
шлаків. Його іноді замінюють гранітом. Плавиковий шпат і двоокис титану
знижують в'язкість і температуру плавлення шлаку, додають йому потрібну
швидкість твердіння. Проте плавиковий шпат в той же час знижує стійкість
горіння дуги, оскільки фтор що входить до його складу здатний утворювати
негативні іони, наявність яких зменшує величину заряду катодної плями,
внаслідок чого для повторного запалення дуги змінного струму потрібна вища
напруга.
Газоутворюючі -
крохмаль, деревна мука, бавовняна пряжа, целюлоза, деревне вугілля, харчова
мука.
Розкислювачі -
феромарганець, феросиліцій, феротитан, феромолібден, алюміній.
Легуючі -
феромарганець, феросиліцій, ферохром, феротитан і рідше оксиди металів (окисли
міді, окисли хрому, вуглекислий нікель і ін.). Основною легуючою речовиною в
більшості покриттів є
феромарганець,
який служить одночасно розкислювачем.
Марганцева руда
також використовується як легуюча речовина в покритті, збільшуючи вміст
марганцю в металі шва. Для легування вуглецем в покриття вводять графіт.
Зв’язні - надають
покриттю вигляду пасти і після твердіння міцно утримують його на стрижні. Для
цієї мети застосовують рідке скло, рідше -декстрин.
Стабілізуючі -
поташ, калієве рідке скло.
Захисні покриття
прийнято класифікувати по вигляду основних речовин, що входять в них і
визначають дію покриття на метал зварювальної ванни. За цією ознакою всі
покриття ділять на 4 групи: руднокислі (Р); рутилові (Т); фтористокальцієві
(Ф); органічні або газозахисні (О).
Руднoкислі
покриття складаються в основному з окислів марганцю, заліза, кремнію. Газовий захист забезпечується органічними
речовинами, що розкладаються в процесі плавлення електроду. Як розкислювач в
покриття вводиться феромарганець.
При зварюванні
електродами з цими покриттями відбувається насичення наплавленого металу киснем
і воднем більшою мірою, чим при фтористокальцієвих покриттях. Тому при
зварюванні низьковуглецевої сталі ударна в'язкість металу шва не перевищує
12-14 кгс·м/см2 , а після старіння знижується на 60-70%. Шви схильні
до утворення тріщин, особливо,
при підвищеному вмісті вуглецю в металі шва. При введенні активних
розкислювачів (кремнію, алюмінію) в дріт або покриття шов може вийти пористим.
Руднокислі покриття не застосовуються для зварювання середньовуглецевих і легованих сталей, а також у поєднанні з дротом із
спокійної сталі. Руднокислі покриття володіють підвищеною токсичністю, оскільки
при плавленні виділяють оксиди марганцю, шкідливі для організму.
Рутилові покриття
як основна шлакоутворююча частина містять від 30 до 50% рутилу (двоокис титану)
з добавками шлакотвірних елементів (польового шпату, магнезиту і ін.). Для
створення газового захисту дуги в покриття вводять від 2 до 8% органічних
речовин - целюлоза, декстрину 15 до 25% карбонатів (мармур, крейда, а для
розкислювання - 15% феросплавів: феромарганець, феросиліцій. Для підвищення коефіцієнта
наплавлення в ці покриття іноді вводять залізний порошок. Рутилові покриття
забезпечують стійке горіння дуги на змінному струмі, малочутливі до зміни
довжини дуги, наявності окалини і іржі, майже не виділяють при зварюванні
шкідливих газів і пари.
Фтористокальцієві
покриття не містять оксидів заліза і марганцю, їх основною частиною є
вуглекислий кальцій (мармур), і плавиковий шпат (флюорит). Як розкислювачі в ці
покриття вводяться феросиліцій, феромарганець, феротитан, алюміній. Для
легування шва може вводитися металева пороша. Фтористокальцієві покриття дають
наплавлений метал з меншим змістом кисню і водню, мало схильний до старіння і
утворення тріщин кристалізацій і холодних, такий, що володіє високою
пластичністю і ударною в'язкістю. Тому електроди з цими покриттями застосовують
при зварці сталі великої товщини і виготовленні відгалужених конструкцій. При
використанні електродів з фтористокальцієвим покриттями дуга повинна бути
гранично короткою. При зварці довгою дугою, а також за наявності на основному
металі іржі, окалини, або при підвищеній вологості покриття метал шва може
виходити пористим. Фтористокальцієві покриття забезпечують підвищене засвоєння
металом шва легуючих домішок – марганець, хром і молібден, які в цьому випадку
майже не вигоряють. Тому всі електроди для зварки легованих сталей і
спеціальних сплавів, а також для наплавлення мають фтористокальцієве покриття.
Недоліком
фтористокальцієвих покриттів є наявність в них плавикового шпату, що знижує
стійкість горіння дуги, тому при зварці ними застосовують постійний струм
зворотної полярності. Для зварки на змінному струмі в ці покриття вводять поташ
або калієве рідке скло, щоб підвищити стійкість горіння дуги.
Органічні (газозахисні)
покриття дають невелику кількість шлаків і тому придатні для зварки
вертикальних, стельових і труднодоступних швів, а також сталі малої товщини (до
3 мм). У захисному середовищі газів міститься багато водню, що забезпечує
відновлення оксидів і покращує якість наплавленого металу, але може викликати
утворення пор. Основними компонентами цих покриттів є харчова мука, целюлоза і
інші органічні речовини.
Кислі
покриття (АНО-2 - Академія наук, інститут
електрозварювання ім. Е. О. Патона, загального призначення, модель - марка 2; СМ-5 - стальмонтаж, модель 5) складаються в основному з оксидів
заліза і марганцю (звичайно у виді руд), кремнезему, феромарганцю.
Рутилові покриття (МР-3; МР-4 - монтажні, рутилові,
моделі 3; 4; АНО-3; АНО-4; ОЗС-3, ОЗС-4, ОЗС-6 – дослідний(опитний) завод з виробництва покритих
електродів, моделі 3; 4; 6 і ін.) мають у своєму складі переважну кількість
рутилу. Наприклад, покриття електрода марки МР-3 складається з рутилу (50%),
тальку, мармуру, каоліну, феромарганцю, целюлози і рідкого скла. Рутилові
покриття при зварюванні менш шкідливі для дихальних органів зварника, чим інші;
шлак на шві утвориться тонкий, швидкотвердіючий і тому рутиловими
електродами можна виконувати шви в будь-якому просторовому положенні.
Целюлозні
покриття (ВСЦ-1, ВСЦ-2 - Всесоюзний науково-дослідний інститут будівництва
трубопроводів, для зварювання, з целюлозою, моделі 1; 2; ОЗЦ-1-1 -
дослідний(опитний) завод, з целюлозою, модель 1 і ін.) складаються з целюлози,
органічної смоли, феросплавів, тальку й ін.
Основні
покриття (УОНИИ-13/45 - універсальна, обмазка науково-дослідного інституту 13 з
тимчасовим опором розривові металу шва не нижче 45 кгс/мм2; ОЗС-2 і
ін.) не містять оксидів заліза і марганцю. Наприклад, покриття марки УОНИИ - 13/45 складається з мармуру, плавикового шпату, кварцового
піску, феросиліцію, феромарганцю, феротитана, рідкого скла.
Метал
шва, виконаний електродами з основним покриттям, володіє відносно великою
ударною в'язкістю, меншою схильністю до старіння й утворення тріщин. Цими
електродами зварюють особливо відповідальні вироби з низьковуглецевої і
легованої сталей. Целюлозні покриття зручні при
зварюванні в будь-якому просторовому положенні, але дають наплавлений метал
зниженої пластичності. Їх застосовують головним чином для зварювання
низкоуглецевої сталі малої товщини.
При
виборі марки електрода для зварювання конструкцій у монтажних умовах варто
враховувати труднощі підтримки постійної довжини дуги, що може привести до
утворення пір у швах. Електроди з основними покриттями дуже чуттєві до зміни
довжини дуги. Тому при монтажному зварюванні часто застосовують електроди з
рутиловм (МР-3) або з рутилоосновным покриттям (СМ-11, АНО-11 і ін).
По
якості, тобто точності виготовлення, стану поверхні покриття і по змісту сірки
і фосфору в наплавленому металі, електроди поділяються на групи 1, 2 і 3. По роду і полярності застосовуваного при зварюванні або
наплавленні струму, а також по номінальній напрузі холостого ходу
використовуваного джерела живлення зварювальної дуги перемінного струму
Електроди позначають з номера 0 до 9 (ДСТ 9466-75).
Класифікація
покритих електродів.
Покриті
електроди для ручного дугового зварювання і наплавлення підрозділяють по
призначенню :
- для зварювання вуглецевих і
низьколегованих конструкційних сталей з тимчасовим опором розривові до 600 МПа, позначаються В;
-
для зварювання легованих
конструкційних сталей з тимчасовим опором розривові понад 600 МПа - Л;
-
для зварювання легованих
теплотривких сталей -Т;
-
для зварювання
високолегованих сталей з особливими властивостями - У;
-
для наплавлення
поверхневих шарів з особливими властивостями - Н.
По
товщині покриття в залежності від відношення діаметра D електрода до діаметра d
сталевого стрижня:
з тонким
покриттям (D/d < 1,20) - М;
із середнім
покриттям (1,20<D/d< 1,45)-C;
з
товстим покриттям (1,45 < D/d <1,80)-Д;
з
особливо товстим покриттям (D/d> 1,80)-Г.
за видом покриття:
- кисле (А);
- рутилове (Р);
- целюлозне (Ц);
- основне (Б);
змішаним
(відповідна подвійна умовна позначка), з іншим покриттям (П).
Типи
покритих електродів для зварювання.
У
позначенні типу електрода входять букви Е (електрод) і цифра, що показує
мінімальний тимчасовий опір розривові металу шва або наплавленого металлу або звареного з'єднання в 107- Па. Буква А після цифрового позначення електродів Е42А,
Е46А, Е50. указує на підвищені пластичність і в'язкість металу шва. Кожен тип
включає кілька марок електродів. Наприклад, до електродів типу Е46 відносяться
марки електродів АНО-3, АНО-4, МР-3, ОЗС-4, ОЗС-6 і ін.
Вибір
типу і марки електрода залежить від марки сталі, що зварюється, товщини листа,
твердості виробу, температури навколишнього повітря при зварюванні,
просторового положення, умов експлуатації звареного виробу й ін. Варто
враховувати, що електроди 3-й групи якості виготовлення створюють при
зварюванні більш щільний метал шва і з меншим змістом сірки і фосфору в ньому.
У
технічних документах (кресленнях, технологічних картах) позначення
характеристики покритих електродів складається з позначення марки, діаметра і
групи електродів. Позначення на етикетках електродної тари більш складне.
Наприклад, електроди типу Е46А за ДСТ 9467-75 марки УОНИИ-13/45 діаметром 3,0 мм для зварювання углеродистых і низьколегованих сталей У с товстим покриттям Д, 2-й групи, із
установленої за ДСТ 9467 - 75
групою індексів 43 2(5), що вказує характеристики наплавленого металу і металу
шва, з основним покриттям Б для зварювання у всіх просторових положеннях 1, на
постійному струмі зворотної полярності позначають 0.
Е46А - УОНИИ-13/45 - 3,0 - УД2
Е43
2(5)-Б 10
ДСТ 9466
- 75, ДСТ 9467 - 75
Тип
електроду визначає міцність металу шва в МПа (наприклад, електроди типів Е50
або Е50А – σв >50 МПа, буква А означає, що
метал шва має підвищені пластичні властивості). Електрод вибирають залежно від
марки сталі зварюваних елементів. Цим забезпечуються передумови до створення
рівномірного з'єднання, також рівноміцність досягається також правильним
вибором технології зварювання і способами контролю якості зварних швів.
Марка електроду
визначається складом захисного покриття і вибирається залежно від роду
зварювального струму (змінний або постійний) і просторового положення шва.
Рекомендовані
електроди при зварюванні вуглецевих та легованих сталей.
При
виготовленні конструкцій із низьковуглецевих сталей широко використовується
ручне зварювання покритими електродами. Залежно від відповідальності
зварюваного виробу користуються електродами типів Э38, Э42, Э42А, Э46, Э46А,
Э50, Э50А. Електроди Э38 використовуються для виготовлення невідповідальних
виробів, Э42 і Э46 - для
відповідальних, а електроди Э42А, Э46А, Э50, Э50А - для особливо відповідальних виробів. При зварюванні сталі
товщиною понад 15 мм і в незручних дла зварника положеннях необхідно
використовувати електроди з підвищеною міцністю наплавленого металу типів Э46,
Э50, Э50А.
Якщо
необхідно одержати однакову міцність наплавленого та основного металу, то тип
електрода підбирають за міцністю основного металу. Наприклад, сталь Ст3сп має границю міцності 380-440 МПа.
Середня границя міцності становить 410 МПа. Вибирають тип електрода Э42, який
забезпечує границю міцності наплавленого металу 420 МПа. Відповідно до типу
електрода (Э42) вибирають його марку.(див. Таблиця 1.пункт 2.2)
Для
підвищення пластичності металу шва та стійкості проти виникнення тріщин
необхідно знижувати глибину проплавлення (діаметр електрода і струм),
використовувати електроди типів Э42А, Э46А, Э50А. Кращі результати дає
застосування електродів із фтористокальцієвим покриттям марок УОНИ-13/45 і УОНИ-13/55,
які забезпечують достатню міцність і високу стійкість металу шва проти
утворення кристалізаційних тріщин.(див.Таблиця 2.пункт 2.2).
Зварювання
конструкційних низковуглецевих сталей проводять електродами з
фтористокальциевыми покриттями мазкий УОНИ-13/45, УОНИ-13/55, УОНИ-13/65,
УОНИ-13/85, G3C-2, ЦУ-1, ДСК-50, УП-1/55, УП-2/55,
К-5А, ЦЛ-18, НИАТ-5 і іншими, що дають щільніший і в'язкіший наплавлений метал,
менш схильний до старіння. Електроди з руднокислими покритями (ОММ-5, ЦМ-7)
застосовувати при зварюванні відповідальних конструкцій з низьколегованих сталей не рекомендовано. Низьколеговані конструкційні сталі краще зварювати
електродами типу Э42А, оскільки метал шва отримує додаткове легування за
рахунок елементів основного, що розплавляється, при цьому метал шва зберігає
високу пластичність. Зварювання електродами типу Э60А дає міцніший, але менш
пластичний метал шва унаслідок вищого вмісту в ньому вуглецю.(див.Таблиця 3.
Пункт 2.2).
2.3 Інструменти,
обладнання та пристосування що використовується при зварювальних роботах
а) Обладнання,
яке використовується при РДЗ покритими електродами.
Устаткування для дугового
зварювання плавленням складається із таких основних видів обладнання:
- механічного зварювального
устаткування (обертачі, маніпулятори, кантувачі, роликові стенди тощо);
- технологічного обладнання;
- джерел живлення;
- систем керування.
Основні
технічні показники джерел живлення зварювальної дуги - зовнішня характеристика,
напруга холостого струму, відносна тривалість роботи (ТР) та відносна
тривалість вмикання (ТВ) у переривистому режимі.
Основним, а деколи і
єдиним видом зварювального устаткування є джерело живлення, яке залежно від
виду електричної енергії і способу її перетворювання може бути віднесене до
одного з таких типів:
- трансформатор - джерело змінного
струму, яке перетворює напругу мережі у знижену змінну напругу, що необхідна
для зварювання;
- генератор - джерело постійного
струму, що перетворює механічну енергію обертання якоря в енергію постійного
струму, що використовують для зварювання;
- перетворювач - джерело постійного
струму, що складається з генератора в комбінації з електродвигуном змінного
струму і яке перетворює енергію напруги мережі живлення в енергію постійного
струму, необхідну для зварювання;
- агрегат - джерело постійного струму,
що складається з генератора і двигуна внутрішнього згоряння, який перетворює
енергію спалювання хімічного палива в енергію постійного струму, що
застосовують для зварювання;
- випрямляч -
джерело постійного струму, що перетворює
енергію напруги мережі у випрямлений постійний струм для зварю
вання.
Усі джерела живлення
класифікують за галузями застосування як загальнопромислові (група О) та
спеціалізовані (група С).
До групи О входять
джерела для ручного дугового зварювання, а також механізованого зварювання під
флюсом та вуглекислому газі, що мають досить просту конструкцію і електричну
схему. До спеціалізованих відносять джерела для зварювання кольорових і легких
металів та їхніх сплавів, тонколистових конструкцій відповідальних виробів
імпульсними і стисненими дугами, що задовольняють не тільки вимогам технології,
але і високого рівня автоматизації зварювального процесу. Це досягається за
рахунок застосування зворотних зв'язків за струмом і напругою, застосуванням
складних електричних схем керування, додаткових спеціальних пристроїв і т. д.
Більшість джерел розраховані на живлення одного зварювального поста. Усі вони
називаються одно постовими, на відміну від багатопостових, які призначені для
одночасного живлення декількох постів.
б) Інструменти та
приладдя електрозварника
Зварювальні пости
комплектують джерелом живлення, електродотримачем, зварювальними проводами,
щитком з світлофільтрами, різними інструментами для зачищання й вимірювання та
іншим приладдям.
Електродотримач - це
пристосування для закріплення електродів і підведення до них струму (рис. 7). За конструкцією електродотримачі
поділяють на:
важільні - ЭР-1 (зварювальний струм 300 А),
ЭР-2 (500 А);
пасатижні - ЭП-2 (250 А),
ЭП-3 (500 А), ЭД-1201(125 А), ЭД-3102(315 А), ЭД-5001(500 А);
защіпні - ЭДС-1201 (125
А), ЭДС-3101 (315 А), ЭУ-3001 (315 А), ЭУ-5001(500А);
гвинтові - ЭВ-2(125 А),
ЭВ-3(315 А), ЭВ -4(500 А).
Електродотримачі мають
відповідати таким вимогам:
- забезпечувати надійне
затискання електродів;
- допускати затискання
електрода не менше ніж у двох положеннях — перпендикулярно та під кутом не
менше 1150 до осі електрода;
- забезпечувати швидку й
легку зміну електродів (4 с);
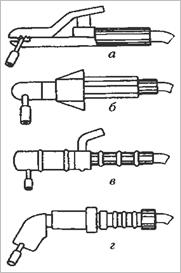
Рис. 7. Електродотримачі:
а - пасатижний; б - гвинтовий; в -
важільний; г – защіпний
- струмоведучі частини
повинні бути надійно ізольовані від випадкового дотику із зварюваними виробами
або руками зварника;
- опір ізоляції має бути
не менше 5 МОм;
рукоятка має бути виготовлена
з ізолюючого матеріалу довжиною не менше 120 мм;
поперечний переріз
рукоятки повинен вписуватися у коло діаметром не більше 40 мм.
Застосування саморобних
електродотримачів забороняється. Електродотримачі повинні витримувати без
ремонту 8 тис. затискань. Проводи (кабелі) призначені для з'єднання
електродотримачів (пальників) із джерелами живлення та підведення зварювального
струму. Використовують гнучкі проводи з мідними або алюмінієвими жилами й
гумовою ізоляцією марок РГД, РГДО, РГДВ, КРПГН, КРПТН, КРПСН, ПРН. Довжина
кабелю при монтажних роботах може становити 40-50 м, але в таких випадках буде значний спад напруги. Допустимим вважається спад напруги до 4 В. Якщо
спад напруги більший за допустимий, то джерело живлення наближають до місця
зварювання або збільшують переріз зварювального проводу. Переріз кабелів
вибирають залежно від сили зварювального струму із розрахунку 5-7 А/мм2
(табл. 4). Кабель складається з великої
кількості відпалених мідних дротів діаметром 0,18-0,20 мм та буває одно- і двожильний.
Таблиця 4. Площа поперечного перерізу зварювальних проводів.
Сила
струму, А |
Площа
поперечного перерізу провода, мм2
|
одинарного |
подвійного |
125 |
25 |
- |
315 |
50 |
2х16 |
500 |
70 |
2х25 |
Зменшення перерізу кабелю
призводить до перегрівання й швидкого
руйнування ізоляції.
Для з'єднання частин
зварювальних кабелів між собою використовують сполучні муфти марок МС-2, МСБ-2,
М-315, М-500 та ін. Для нероз'ємного з'єднання кабелів застосовують з'єднувачі
типу ССП - 2. До
джерела живлення кабель можна підключати через приєднувальну муфту МС-3.
Зворотний кабель приєднують клемами заземлення типу КЗ-2 та КЗП-12. Зворотним
проводом можуть служити сталеві шини, зварювальні плити, стелажі й сама
конструкція, якщо їх переріз забезпечує безпечне за умовами нагрівання
проходження зварювального струму. Окремі елементи, які використовуються в
якості зворотного проводу, повинні бути з'єднані між собою болтами, струбцинами
або затискачами. При проведенні зварювальних робіт в пожежо- і
вибухонебезпечних приміщеннях зворотний провід від виробу до джерела живлення
має бути тільки ізольованим. Не допускається з'єднання проводів на скрутках. В
обертових виробах для під'єднання зворотного кабелю використовують ковзний
контакт. Довжина проводів між живильною мережею і пересувними зварювальними
агрегатами не повинна перевищувати 10 м. Проводи (кабелі) слід захищати від
механічних пошкоджень, контакту з водою, маслами, сталевими канатами, шлангами
з горючими газами і гарячими трубопроводами.
Для роботи зварника
випускаються спеціальні комплекти (КИ-125, КИ-315, КИ-500), які містять
електродотримачі, сполучну муфту, зварювальний кабель, запасні частини до
електродотримача, світлофільтри, затискачі, шлаковіддільник, металеву щітку.
Виготовляють також набори інструментів ЭНИ-300 та ЭНИ-300/1 до комплекту яких
входять електродотримач, клема заземлення, сполучна муфта, щітка-зубило,
викрутка, плоскогубці, розвідний ключ, клеймо, молоток, світлофільтри, відрізок
кабелю (3 м).
Для виконання
зварювальних робіт зварник повинен мати й допоміжний інструмент: молоток,
зубило, напилки, сталеву щітку, шаблони, кутник, метр, висок, лінійку. Інколи
зварювальний пост обладнують шліфувальною машиною, спеціальними кромкорізами,
дрелями та ін. Інструменти та електроди слід зберігати в ящиках, сумках або
пеналах. Для просушування електродів використовують спеціальні печі, шафи й
пенали.
Для захисту очей та
обличчя зварника від променів електричної дуги і бризок розплавленого металу
застосовують щитки або маски із спеціальними світлофільтрами. їх виготовляють
із чорної фібри або спеціальної пластмаси. Залежно від сили зварювального
струму щитки й маски оснащені світлофільтрами, які виготовляють із
темно-синього скла марки ТС-ЗС двох видів: світлофільтри для нормального огляду
(розмір 52x102 мм) і збільшеного (90x102 мм) з товщиною від 1,5 до 4,0 мм. Із зовнішнього боку світлофільтри захищають від бризок розплавленого металу віконним склом
товщиною 2,5 мм, яке при забрудненні міняють. Категорично забороняється
замінювати світлофільтри саморобним пофарбованим склом. Світлове випромінювання
дуги має послаблюватися світлофільтрами в 102-106 разів. Нині в СНД
використовують світлофільтри серії С, які поділяються на 13 класів. Вони
забезпечують захист очей від випромінювання при зварюванні на струмах від 5 до
1000 А. Світлофільтри підбирають залежно від характеру робіт та сили
зварювального струму.
Робітники, які виконують
допоміжні роботи, для захисту очей використовують світлофільтри типу В (В-1,
В-2, В-3).
Сучасна
індустрія охорони праці у зварювальному виробництві пропонує великий вибір
зварювальних масок. Вони мають зручну конфігурацію, малу масу, забезпечують
тепловий захист голови і захисту очей від світлового випромінювання
зварювальної дуги. Практично у всіх масках забезпечене швидке автономне
затемнення огляді того вікна залежно від величини зварювального струму.
Розділ 3. Техніка
безпеки
3.1
Заходи промислової санітарії, техніки безпеки та протипожежної безпеки
Створення
безпечних умов праці є основною і найважливішою задачею будь-якого виробництва.
За правильну організацію і стан техніки безпеки несе відповідальність
керівництво підприємства, а всі поточні питання вирішуються відділами техніки
безпеки або інженерами по техніці безпеки.
Дотримання
Правил техніки безпеки на підприємствах контролюється інспекцією Держтехнягляду
України, інспектором ЦК профспілок робітників даної галузі промисловості,
Державною санітарною інспекцією і Державною інспекцією пожежної охорони.
Крім
загальних положень необхідно враховувати деякі спеціальні правила по техніці
безпеки при зварюванні металів і санітарних умов. Відповідно до трудового
законодавства до зварювальних робіт допускаються особи не молодше 18 років;
зварники мають додаткову відпустку тривалістю до 12 робочих днів; при роботі
всередині посудин робочий день зварювальника обмежений до шести годин.
Кожен
зварювальник повинен у досконалості знати правила техніки безпеки, проходити
інструктаж перед допуском до роботи, здавати відповідні іспити.
При
виконанні зварювальних робіт можуть відбуватися нещасні випадки по наступних
причинах: поразка електричним струмом, шкідливий вплив світлового
випромінювання електричної дуги, опіки від бризів розплавленого металу і шлаку,
забруднення повітря продуктами горіння зварювальної дуги, вибухи судин і
вибухонебезпечних речовин, недотримання протипожежних правил.
Електричний
струм уражає нервову систему людини або викликає опіки. Ступінь враження залежить
від сили струму, його напруги й опору тіла людини. Величина струму до 0,002 А
не представляє небезпеки, струм від 0,002 до 0,05 А небезпечний, може викликати
болючі відчуття, сприяє різкому скороченню м'язів, а вище 0,05 А може привести
до смертельного результату.
У
сухих приміщеннях безпечним вважається напруга до 36 А, а в сирих до 12 А, що
необхідно враховувати при проводці лінії для освітлювальних цілей.
Промені
електричної дуги шкідливо впливають на зварювальників і людей, які знаходяться
поруч з ними. За своїми властивостями вони поділяються на видимі і невидимі.
До
видимих відносять світлові промені електричної дуги, які осліпляюче діють на
очі. При довгочасному опроміненні послаблюють зір.
До
невидимих відносять ультрафіолетові і інфрачервоні промені, які визивають
запалення очей і опіки шкіри.
Ультрафіолетові
промені шкідливо діють на сітчатку і рогівку очей. Якщо на протязі декількох
хвилин дивитись на світло дуги без захисних засобів, то через деякий час
появляється світлобоязкість, сльозоточивість і сильні болі в очах. Складається
враження, що очі забруднені піском. Невеликі запалення очей проходять через
кілька годин. Інфрачервоні промені при тривалій дії викликають захворювання
очей, сприяють загальній утраті зору (катаракта крихталика).
Крім
опіків від електричної дуги (ультрафіолетовими променями) при зварюванні можуть
бути опіки від бризг розплавленого металу і шлаку.
Для
попередження опіків зварникові необхідно:
-
мати спецодяг із брезенту або щільного сукна;
-
не заправляти куртку в штани, а штани в чоботи, не робити на спецодязі відкриті
кишені;
-
прикривати голову беретом або будь-яким головним убором без козирка.
-
працювати в рукавицях;
-
забезпечувати мінімальне розбризкування металу шляхом відповідного підбору
режимів зварювання;
-
зачищати шви після повного остигання шлаку, оглядати шви після зварювання і
зачищати їх тільки в окулярах із простим склом;
-
при зварюванні вертикальних і стельових швів надягати азбестові нарукавники і
щільно перев'язувати їх поверх рукавів.
У
зварювальних цехах, на будівельно-монтажних площадках, на зварювальних і
наплавочних ділянках необхідно суворо дотримуватися наступні правила, що
запобігають можливість виникнення пожеж від іскор, що розлітаються, і бризг
розплавленого металу:
-
робоче місце зварника повинно бути цілком очищене від легкозаймистих або
вибухонебезпечних матеріалів. Легкозаймисті рідини і різні пальні матеріали
повинні знаходитися від місця зварювання на відстані не менш 30 м, ацетиленові генератори і балони з пальними газами — на відстані не менш 10 м;
-
у місцях виконання зварювальних робіт захист від іскор, що розлітаються, і
бризг металу повинна забезпечуватися металевими або брезентовими ширмами, на
ділянках зварювання повинні бути вогнегасники, шухляди з піском, бочки з водою,
різний пожежний інвентар, обов'язково телефонний зв'язок і пристрої для
звукових сигналів;
- усі робітники
та службовці при влаштуванні на роботу або при зміні робочих місць повинні бути
проінструктовані з протипожежної безпеки і по принятому на підприємстві
протипожежному режимі. На великих ділянках і в цехах повинні бути офіційно
назначені відповідальні за стан протипожежних засобів і виконання
протипожежного режиму роботи.
Список
використаних джерел
1.
Биковський
О.Г., Піньковський І. В. Довідник зварника. –К.: Техніка, 2002. – 336 с.
2.
Глизманенко Д.Л. Газове
зварювання та різання металу.-К.:Техніка, 1971.
3.
Гуменюк
І.В. Обладнання і технологія газозварювальних робіт. –К.: Грамота, 2005.
4.
Технология
металлов и сварка. Учебник для вузов. Под ред. П. И. Полухина. М., «Высшая школа»,1977.
5.
Рыбаков В. М.
Дуговая и газовая сварка:.- М.: Высшая
школа, 1981.
6.
Сапиро. Л. С. Справочник сварщика:
Пособие для сварщиков, мастеров,технологов,конструкторов.-2-е изд.,перераб. и
доп.-Донецк:Донбас,1978.
7.
Сварщик.-1999-2006.
-№№ 1-6.
8.
Соколов И.И. Газовая
сварка и резка металлов.-М.: Высшая школа, 1986.
9.
Стеклов
О.І. Основи зварювального виробництва.- К.:Вища школа, 1990.
|